TPWG315 380 DIGITALE DRUKMETER
Kort
Samen met de eigenschap van PE-materiaal dat voortdurend wordt geperfectioneerd en verhoogd, worden PE-buizen op grote schaal gebruikt in de gas- en watervoorziening, rioolwaterzuivering, de chemische industrie, de mijne enzovoort.
Onze fabriek heeft meer dan tien jaar onderzoek gedaan naar en ontwikkeld voor de stompfusiemachine uit de TPW-serie, die geschikt is voor PE, PP en PVDF.
Tegenwoordig omvatten onze producten acht soorten en meer dan 20 typen die van toepassing zijn op de constructie van kunststofbuizen en die als volgt in de werkplaats worden gemaakt:
SHS-serie socketlasapparaat | TPWC-serie Lintzaag |
Handmatige stomplasmachine uit de TPW-serie | Werkplaatslasmachine uit de TPWG-serie |
Buttfusion-machine uit de TPWY-serie | Serie speciaal gereedschap |
QZD-serie Auto-butt-fusion-machine | SHM-serie zadelfusiemachine |
Deze handleiding is bedoeld voor de TPWG315 lasmachine voor kunststofbuizen in de werkplaats. Om elk soort ongeval veroorzaakt door elektrische of mechanische schade te voorkomen. Het wordt aanbevolen om de volgende veiligheidsregels aandachtig te lezen en te volgen voordat u de machine gebruikt.
Speciale beschrijving
Alvorens de machine te gebruiken, moet iedereen deze beschrijving aandachtig lezen en goed bewaren om de veiligheid van de uitrusting en de bediener en die van anderen te garanderen.
2.1 De machine wordt gebruikt voor het lassen van buizen gemaakt van PE, PP, PVDF en kan niet worden gebruikt voor het lassen van materiaal zonder beschrijving, anders kan de machine beschadigd raken of kan er een ongeluk gebeuren.
2.2 Gebruik de machine niet op een plaats met potentieel explosiegevaar
2.3 De machine moet worden bediend door verantwoordelijk, gekwalificeerd en opgeleid personeel.
2.4 De machine moet op een droge plaats worden gebruikt. De beschermende maatregelen moeten worden genomen als het apparaat wordt gebruikt in de regen of op natte grond.
2.5 De machine had een voeding van 380 V ± 10%, 50 Hz nodig. Als er verlengkabels moeten worden gebruikt, moet er voldoende doorsnede zijn in overeenstemming met hun lengte.
Veiligheid
3.1 veiligheidsmarkeringen
De volgende markeringen zijn op de machine aangebracht:
3.2 Voorzorgsmaatregelen voor de veiligheid
Wees voorzichtig bij het bedienen en transporteren van de machine volgens alle veiligheidsregels in deze instructie.
3.2.1 Let op bij gebruik
l De operator moet verantwoordelijk en opgeleid personeel zijn.
l Inspecteer en onderhoud de machine jaarlijks volledig op de veiligheid en de machine
betrouwbaarheid.
3.2.2Stroom
De elektriciteitsverdeelkast moet een aardlekschakelaar hebben met de relevante elektriciteitsveiligheidsnorm. Alle veiligheidsvoorzieningen zijn aangegeven met gemakkelijk te begrijpen woorden of markeringen.
3.2.3 Schakel de stroom uit voordat u de veiligheidsafdekking of het net verwijdert.
Aansluiting van machine op stroom
De kabel die de machine met de stroom verbindt, moet bestand zijn tegen mechanische schokken en chemische corrosie. Als de verlengde draad wordt gebruikt, moet deze voldoende kabeldoorsnede hebben, afhankelijk van de lengte.
Aarding: De hele locatie moet dezelfde aarddraad hebben en het aardverbindingssysteem moet door professionele mensen worden voltooid en getest.
3.2.3Opslag van elektrische apparatuur
Voor de min. gevaren, moet alle apparatuur als volgt correct worden gebruikt en opgeslagen:
※Vermijd het gebruik van tijdelijke draad die niet aan de norm voldoet
※ Raak de elektroforeonderdelen niet aan
※ Verbied het loskoppelen van de kabel
※ Verbied het slepen van kabels voor hijsapparatuur
※ Plaats geen zware of scherpe voorwerpen op de kabels en controleer de temperatuur van de kabel binnen de limiettemperatuur (70℃)
※ Werk niet in een natte omgeving. Controleer of de groef en schoenen droog zijn.
※ Spat niet op de machine
3.2.4 Controleer periodiek de isolatieconditie van de machine
※ Controleer de isolatie van kabels, vooral de geëxtrudeerde punten
※ Gebruik de machine niet onder extreme omstandigheden.
※ Controleer minimaal per week of de lekkageschakelaar goed werkt.
※ Controleer de aarding van de machine door gekwalificeerd personeel
3.2.5 Reinig en controleer de machine zorgvuldig
※Gebruik geen materialen (zoals schuurmiddelen en andere oplosmiddelen) die de isolatie gemakkelijk beschadigen bij het reinigen van de machine.
※ Zorg ervoor dat de stroom is uitgeschakeld wanneer u de taak voltooit.
※Zorg ervoor dat er geen schade aan de machine is voordat u deze opnieuw gebruikt.
Als u alleen het bovengenoemde volgt, kan de voorzorgsmaatregel goed werken.
3.2.6 Beginnen
Zorg ervoor dat de schakelaar van de machine gesloten is voordat u deze inschakelt.
3.2.7 Dichtheid van onderdelen
Zorg ervoor dat de leidingen correct zijn bevestigd. Zorg ervoor dat hij goed kan bewegen en voorkom dat hij naar beneden glijdt.
3.2.8 Werkomgeving
Vermijd het gebruik van de machine in een omgeving vol verf, gas, rook en olie, omdat hierdoor infecties aan ogen en luchtwegen kunnen ontstaan.
Zet de machine niet op een vuile plaats.
3.2.9 Veiligheid van het personeel tijdens het werken
Verwijder sieraden en ringen en draag geen loszittende kleding. Vermijd het dragen van schoenveters, lange snorren of lang haar dat in de machine kan worden gehaakt.
3.3 Veiligheid van apparatuur
De hydraulische werkplaatslasmachine mag alleen worden bediend door een professional of werknemer met een opgeleid certificaat. Een leek kan de machine of anderen in de buurt beschadigen.
3.3.1 Verwarmingsplaat
l De oppervlaktetemperatuur van de verwarmingsplaat kan 270 ℃ bereiken. Raak deze nooit rechtstreeks aan om verbranding te voorkomen
l Reinig het oppervlak voor en na gebruik met een zachte doek. Vermijd schurende materialen die de coating kunnen beschadigen.
l Controleer de kabel van de verwarmingsplaat en controleer de oppervlaktetemperatuur.
3.3.2 Schaafgereedschap
l Voordat de pijpen worden geschoren, moeten de uiteinden van de pijpen worden schoongemaakt, vooral het zand of andere tocht die rond de uiteinden kraait. Door dit te doen, kan de levensduur van de rand worden verlengd en wordt ook voorkomen dat de spaanders worden weggegooid en mensen in gevaar worden gebracht.
Zorg ervoor dat het schaafgereedschap stevig vastzit aan de twee buisuiteinden
3.3.3 Mainframe:
Zorg ervoor dat de leidingen of fittingen correct zijn bevestigd om de juiste uitlijning te verkrijgen.
l Bij het verbinden van buizen moet de operator een bepaalde ruimte tot de machine vrijhouden voor de veiligheid van het personeel.
l Zorg er vóór het transport voor dat alle klemmen goed vastzitten en tijdens het transport niet naar beneden kunnen vallen.
Toepasselijk bereik en technische parameters
Type | TPWG315 | |
Materialen voor lassen | PE, PP, PVDF | |
Buiten Diameter bereiken | elleboog (DN, mm) | 90 110 125 140 160 180 200 225 250 280 315mm |
T-stuk (DN, mm) | 90 110 125 140 160 180 200 225 250 280 315mm | |
kruis (DN, mm) | 90 110 125 140 160 180 200 225 250 280 315mm | |
Wyes 45°& 60° (DN, mm) | 90 110 125 140 160 180 200 225 250 280 315mm | |
Omgevingstemperatuur | -5~45℃ | |
Hydraulische olie | 40~50 (kinematische viscositeit) mm2/s, 40℃) | |
Voeding | ~380 V±10% | |
Frequentie | 50 Hz | |
Totale stroom | 13 EEN | |
Totaal vermogen | 7,4 kW | |
Inclusief verwarmingsplaat | 5,15 kW | |
Motor voor schaafgereedschap | 1,5 kW | |
Hydraulische unitmotor | 0,75 kW | |
Isolerende weerstand | >1MΩ | |
Max. hydraulische druk | 6 MPa | |
Totale sectie cilinders | 12,56 cm2 | |
Max. temperatuur van verwarmingsplaat | 270℃ | |
Verschil in oppervlaktetemperatuur van verwarmingsplaat | ± 7℃ | |
Ongewenst geluid | <70 dB | |
Olietankvolume | 55L | |
Totaal gewicht (kg) | 995 |
Beschrijvingen
De werkplaatslasmachine kan de elleboog, het T-stuk, het kruis door PE-buis in de werkplaats produceren. De standaard klemmen voldoen aan de standaard leidingmaten volgens ISO161/1.
5.1 Hoofdmachine
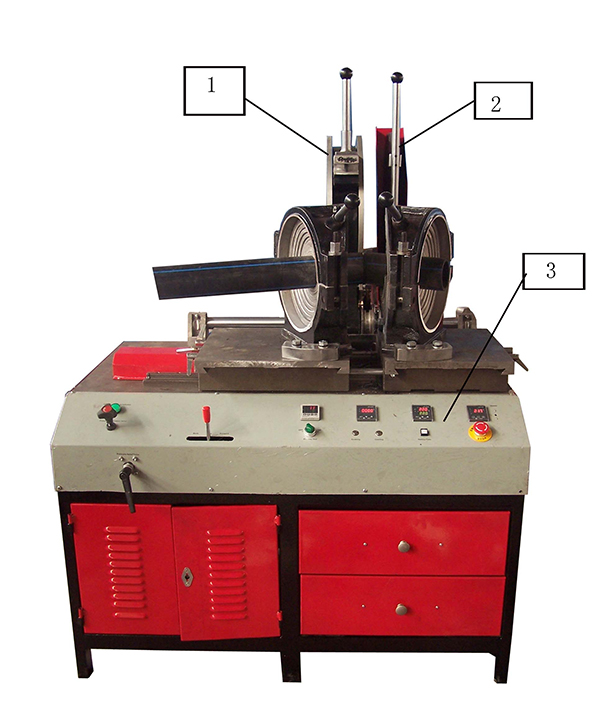
1. Planningstool | 2. Verwarmingsplaat | 3. Bedieningspaneel |
5.2 Bedieningspaneel
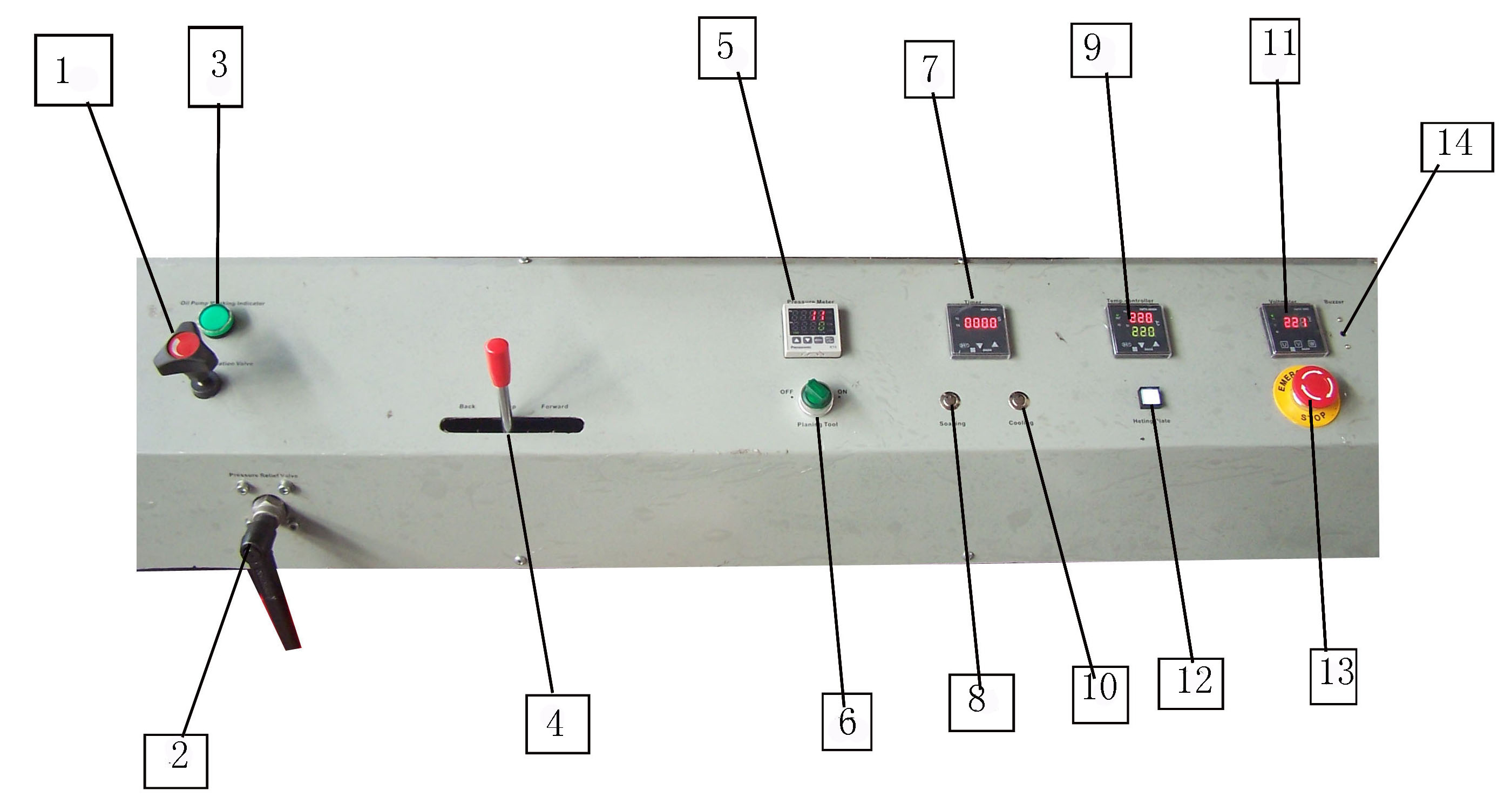
1. Drukregelklep | 2. Overdrukventiel | 3. Werkindicator oliepomp | 4. Richtingsklep |
5. Digitale drukmeter | 6. Planeerknop | 7. Timer | 8. Knop voor inweektijd |
9. Temperatuurcontrolemeter | 10. Knop voor koeltijd | 11. Voltmeter | 12. Verwarmingsschakelaar |
13. Noodstop | 14. Zoemer |
Installatie
6.1 Hijsen en installeren
Houd de machine bij het optillen en installeren horizontaal en kantel of keer hem nooit om ongewenste schade te voorkomen.
6.1.1 Als er een vorkheftruck wordt gebruikt, moet deze voorzichtig vanaf de onderkant van de machine worden ingestoken om beschadiging van de olieslang en het circuit te voorkomen
6.1.2 Bij het transporteren van de machine naar de installatiepositie moet het hoofdframe stabiel en horizontaal worden gehouden.
6.1.3 Installeer de motor op de reductiekast van het schaafgereedschap en bevestig deze met schroeven, weergegeven in Afb. 3.
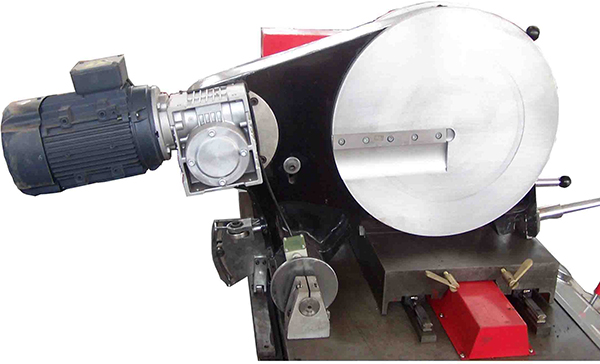
6.2 Verbinding
Zorg ervoor dat er voldoende ruimte is om de machine te plaatsen, houd de hele machine horizontaal en zorg voor de juiste aansluiting van alle stopcontacten, kabels en slangen bij het installeren van de machine.
6.2.1 Sluit de hoofdmachine aan op de elektriciteitskast.
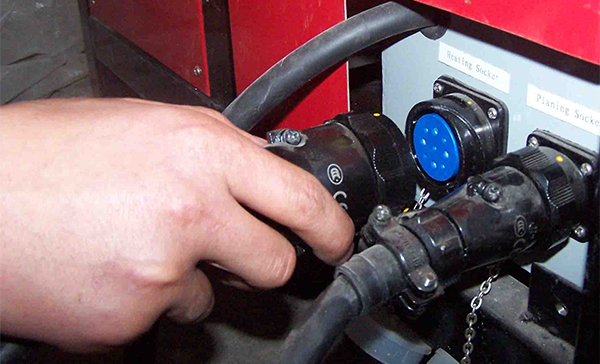
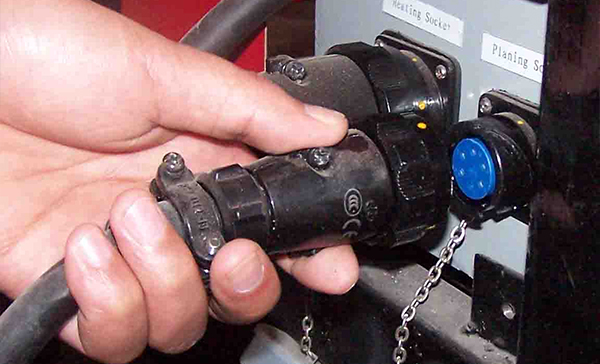
Afb. 4 Sluit de verwarmingsplaat aan op de elektriciteitskast
Afb. 5 Sluit de planningstool aan op de elektriciteitskast
6.2.2 De kabel van de machine aansluiten op de stroom, die drie fasen heeft: vijf draden 380V 50HZ.
Om veiligheidsredenen moet de machine worden geaard vanaf het aardpunt van de machine.
6.2.3 Vul de gefilterde hydraulische olie bij. De hoogte van de olie moet meer dan 2/3 van de hoogte van de inhoudsmeter bedragen.
Waarschuwing: Aarding moet door professionele mensen worden uitgevoerd.
Gebruiksaanwijzing
Volg alle veiligheidsregels op de machine. Ongetrainde personen mogen de machine niet bedienen.
7.1 Vermogen
Sluit de aardlekschakelaar
7.2 Start de oliepomp
Start de oliepomp en let op de draairichting. Als de manometer meetwaarden weergeeft, is de rotatie juist. Als dit niet het geval is, verwissel dan twee stroomvoerende draden.
7.3 Controleer en pas de sleepdruk en bewegingssnelheid van de sleepplaat aan. De werkdruk van het systeem bedraagt 6 MPa. De verbindingsdruk kan worden aangepast via de drukregelklep op het bedieningspaneel. De schaafdruk moet geleidelijk worden verhoogd en behouden wanneer er aanhoudende spaanders verschijnen (niet te groot). De voedingssnelheid van de sleepplaat kan worden aangepast via de terugslagklep (in de basis).
7.4 Klemmen installeren
Installeer de linker en rechter klemzittingen (klemmen voor T-stukken of ellebogen) volgens de te vervaardigen fittingen.
1) Zet ze eerst vast met de borgpen die aan de machine is bevestigd;
2) Pas de hoek aan met de speciale locatiehandgreep;
3) Draai de borgschroef vast met een sleutel.
Als de elleboogklemmen moeten worden gebruikt, druk ze dan stevig aan met de borgplaat nadat u de hoek hebt aangepast.
7.5 Stel de gespecificeerde temperatuur in op de temperatuurregelaar volgens het pijplasproces. (Zie paragraaf 7.10)
7.6 Voordat u het schaafgereedschap omhoog of omlaag brengt, moet u de vergrendeling op de handgreep openen.
7.7 Leidingen in de machine plaatsen
7.7.1 Scheid de klemmen van de machine door op de hendel van de richtingsklep te drukken
7.7.2 Plaats de buizen in de klemmen en zet ze vast; de ruimte tussen twee buisuiteinden moet voldoende zijn voor het schaafgereedschap.
7.7.3 Vergrendel de overdrukklep, terwijl u de twee uiteinden sluit, draai de drukregelklep totdat de manometer de smeltdruk aangeeft, die wordt bepaald door de buismaterialen.
7.8 Schaven
7.8.1 Scheid de klemmen door op de richtingsklep en de volledig geopende overdrukklep te drukken.
7.8.2 Plaats het schaafgereedschap tussen de twee pijpuiteinden en schakel het in, benader de pijpuiteinden in de richting van het planningshulpmiddel door op de richtingsklep “vooruit” te drukken en pas het drukregelventiel aan om de juiste druk te behouden totdat er continu spaanders uit de twee pijpen verschijnen zijkanten.Opmerking: 1) De dikte van de spaanders moet binnen 0,2 ~ 0,5 mm liggen en kan worden gewijzigd door de hoogte van het schaafgereedschap aan te passen.
2) De schaafdruk mag niet hoger zijn dan 2,0 MPa om schade aan het planningshulpmiddel te voorkomen.
7.8.3 Na het schaven de klemmen losmaken en het planningshulpmiddel verwijderen.
7.8.4 Sluit de twee uiteinden om ze uit te lijnen. Als de verkeerde uitlijning groter is dan 10% van de buisdikte, verbeter deze dan door de bovenste klemmen los of vast te draaien. Als de opening tussen de uiteinden groter is dan 10% van de wanddikte van de buis, moet u de buis opnieuw schaven totdat u aan de vereiste voldoet.
7.9 Lassen
7.9.1 Stel de inweektijd en afkoeltijd in afhankelijk van het lasproces.
7.9.2 Nadat u het schaafgereedschap hebt verwijderd, plaatst u de verwarmingsplaat, vergrendelt u geleidelijk de overdrukklep terwijl u de voorwaartse richtingsklep duwt, waardoor de verwarmingsdruk wordt verhoogd tot de gespecificeerde smeltdruk(P1). De buisuiteinden blijven aan de verwarmingsplaat plakken en het versmelten begint.
7.9.3 Wanneer zich een kleine kraal ophoopt, duwt u de richtingsklep in het midden terug om de druk te behouden. Draai de terugslagklep om de druk te verlagen tot de weekdruk(P2) en vergrendel het vervolgens snel. Druk vervolgens de inweektijdknop in om de tijd in te stellen.
7.9.4 Na het weken (de zoemer gaat af) opent u de klemmen door op de richtingsklep te drukken en verwijdert u de verwarmingsplaat snel.
7.9.5 Verbind de twee gesmolten uiteinden snel en houd de richtingsklep een korte tijd op “vooruit” en druk dan terug naar de middelste positie om de druk te behouden. Op dit moment zijn de waarden op de manometer de ingestelde smeltdruk (zo niet, pas deze dan aan door op de drukregelklep te drukken).
7.9.6 Druk de koeltijdknop in wanneer het koelen begint. Nadat de afkoeltijd is verstreken, klinkt er een zoemer. Beleef de systeemdruk opnieuw door op het overdrukventiel te drukken, open de klemmen en verwijder de verbindingen.
7.9.7 Controleer de verbinding volgens de lasprocesnormen.
7.10 Temperatuurregelaar en timer
7.10.1 Timerinstelling
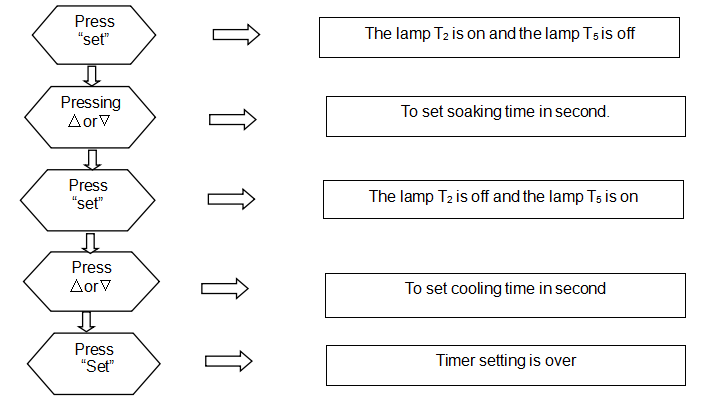
7.10 Temperatuurregelaar en timer
7.10.1 Timerinstelling
7.10.2 Timer gebruiken
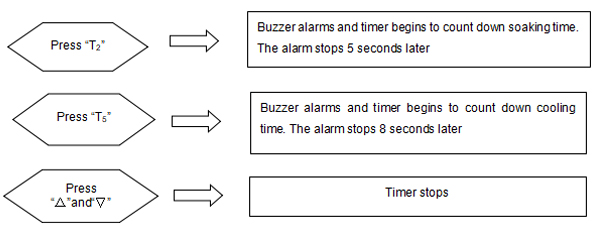
7.10.3 Instelling temperatuurregelaar
1) Druk langer dan 3 seconden op “SET” totdat “sd” in het bovenste venster verschijnt
2) Druk op “∧” of “∨” om de waarde te wijzigen naar de opgegeven temperatuur (druk continu op “∧” of “∨”, de waarde wordt automatisch plus of min)
3) Druk na het instellen op “SET” om terug te gaan naar de monitoring- en besturingsinterface
Referentie lasnorm (DVS2207-1-1995)
8.1 Vanwege verschillende lasnormen en PE-materialen zijn de tijd en druk van de fase van het fusieproces verschillend. Het suggereert dat de werkelijke lasparameters moeten worden bewezen door fabrikanten van buizen en fittingen
8.2 Gezien de lastemperatuur van buizen gemaakt van PE, PP en PVDF varieert de DVS-standaard van 180 ℃ tot 270 ℃. De toepassingstemperatuur van de verwarmingsplaat ligt binnen 180 ~ 230 ℃ en de Max. oppervlaktetemperatuur kan 270℃ bereiken.
8.3 ReferentiestandaardDVS2207-1-1995
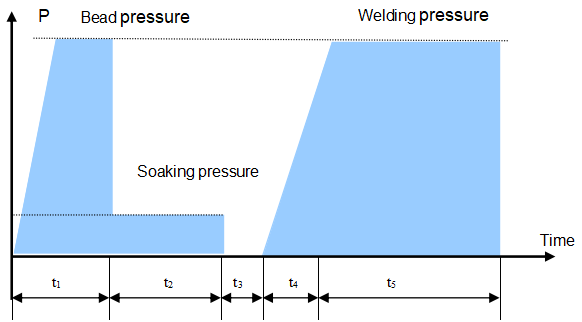
Wanddikte (mm) | Kraalhoogte (mm) | Kraalopbouwdruk (MPa) | Inweektijd t2(Sec) | Weekdruk (MPa) | Omschakeltijd t3(sec) | Drukopbouwtijd t4(sec) | Lasdruk (MPa) | Koeltijd t5(min) |
0~4,5 | 0,5 | 0,15 | 45 | ≤0,02 | 5 | 5 | 0,15±0,01 | 6 |
4,5~7 | 1,0 | 0,15 | 45~70 | ≤0,02 | 5~6 | 5~6 | 0,15±0,01 | 6~10 |
7~12 | 1.5 | 0,15 | 70~120 | ≤0,02 | 6~8 | 6~8 | 0,15±0,01 | 10~16 |
12~19 | 2.0 | 0,15 | 120~190 | ≤0,02 | 8~10 | 8~11 | 0,15±0,01 | 16~24 |
19~26 | 2.5 | 0,15 | 190~260 | ≤0,02 | 10~12 | 11~14 | 0,15±0,01 | 24~32 |
26~37 | 3.0 | 0,15 | 260~370 | ≤0,02 | 12~16 | 14~19 | 0,15±0,01 | 32~45 |
37~50 | 3.5 | 0,15 | 370~500 | ≤0,02 | 16~20 | 19~25 | 0,15±0,01 | 45~60 |
50~70 | 4.0 | 0,15 | 500~700 | ≤0,02 | 20~25 | 25~35 | 0,15±0,01 | 60~80 |
Opmerking: De opbouwdruk en lasdruk in de vorm zijn de aanbevolen interfacedruk, de manometerdruk moet worden berekend met de volgende formule.

De procedure voor het aanbrengen van fabricage
9.1 Elleboog maken
9.1.1 Afhankelijk van de hoek van de elleboog en het aantal lasonderdelen, kan de lashoek tussen elk onderdeel worden bepaald.
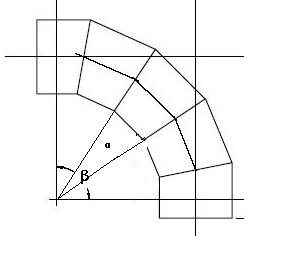
Uitleg: α - lashoek
β - ellebooghoek
n - aantal segmenten
Bijvoorbeeld: de 90°-elleboog is verdeeld in vijf te lassen segmenten, de lashoek α=β/(n-1)=90°/(5-1)=22,5°
9.1.2 De minimale afmeting van elk lasonderdeel in de hoeveelheden lasonderdelen wordt door de lintzaag volgens de hoek gesneden.
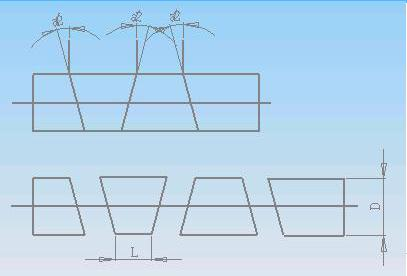
Uitleg:
D - buitendiameter van de buis
L - Min. lengte van elk onderdeel
9.2 De procedure voor het produceren van T-shirts
9.2.1 De materialen zijn als het volgende diagram:
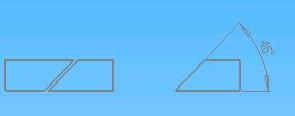
9.2.2 Lassen als diagramstructuur:
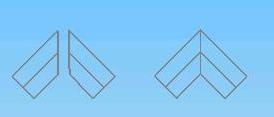
9.2.3 Een hoek wordt gesneden zoals in het diagram
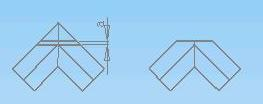
Opmerking: De afmeting “a” mag niet kleiner zijn dan 20㎜, wat overeenkomt met de planningsmarge en de compenserende smeltbare kraal.
9.2.4 Lassen als diagramstructuur, de T-stukken zijn geproduceerd.
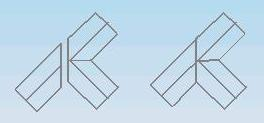
9.3 De procedure voor het maken van dwarspijpen met gelijke diameter
9.3.1 De materialen worden gesneden zoals in het volgende diagram
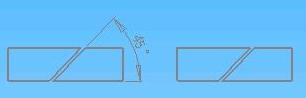
9.3.2 De twee koppelingen zijn gelast volgens de diagramstructuur:
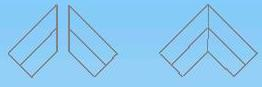
9.3.3 Een hoek wordt gesneden zoals in het diagram:
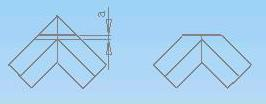
Opmerking: De afmeting "a" mag niet kleiner zijn dan 20㎜, wat de planningsmarge is en de smeltbare kraal compenseert.
9.3.4 Gelast als diagramstructuur.
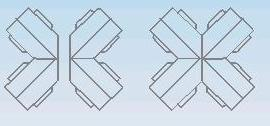
9.4 De procedure voor het vervaardigen van “Y”-vormige fittingen (45° of 60°)
9.4.1 snijden volgens de volgende tekening (neem als voorbeeld 60° “Y”-vormige fittingen)
9.4.2 Ga verder met het eerste lassen volgens de volgende tekeningen:
9.4.3 Pas de klemmen aan en ga verder met het tweede laswerk.
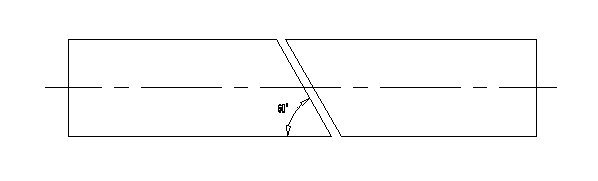
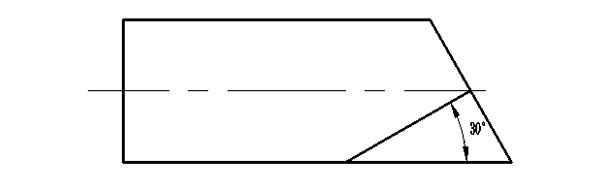
9.5 overige fittingen lassen
9.5.1. Pijp met pijp
9.5.2. Pijp met fitting
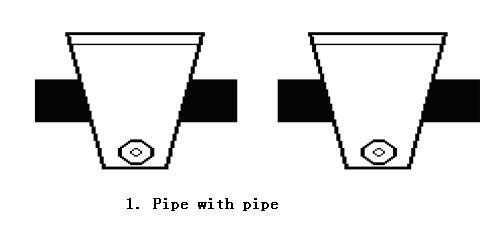
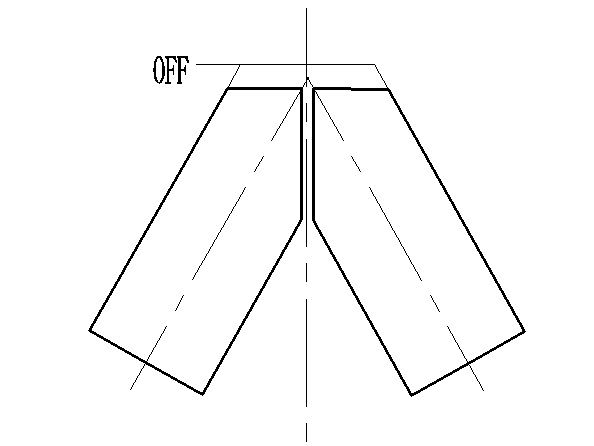
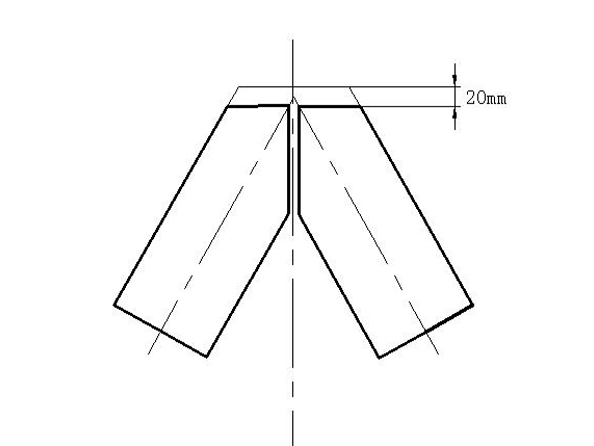
9.5.3 Montage met fitting
9.5.4 Montage met stompflens
9.5.5 Buis met stompflens
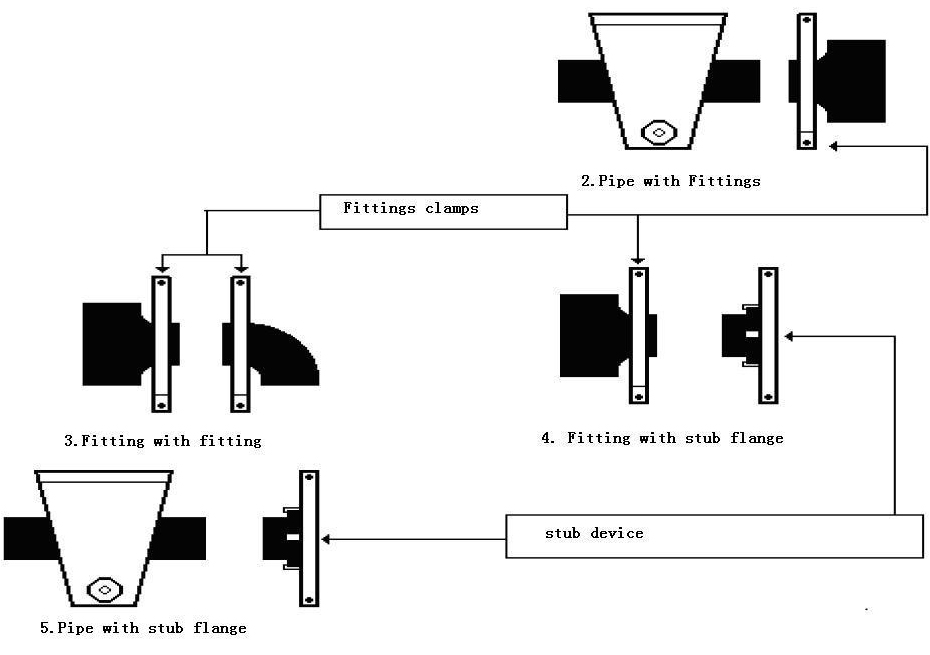
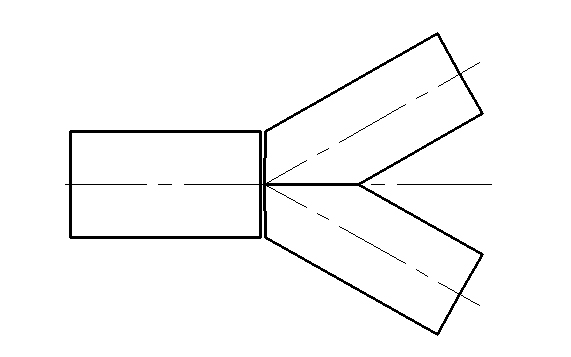
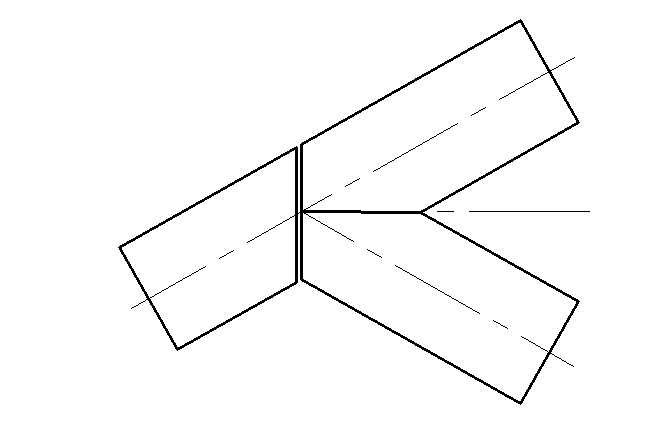
Storingen analyseren en oplossen
10.1 Analyse van frequente problemen met de kwaliteit van gewrichten:
10.2 Onderhoud
uuPTFE-gecoate verwarmingsplaat
Wees voorzichtig bij het hanteren van de verwarmingsspiegel om schade aan de PTFE-coating te voorkomen.
Houd de met PTFE gecoate oppervlakken altijd schoon. Reiniging moet worden uitgevoerd terwijl het oppervlak nog warm is, met behulp van een zachte doek of papier. Vermijd schurende materialen die de met PTFE gecoate oppervlakken kunnen beschadigen.
Op regelmatige tijdstippen raden wij u aan:
- Reinig de oppervlakken met een snel verdampend reinigingsmiddel (alcohol)
- Controleer het aandraaien van de schroeven en de toestand van de kabel en de stekker
u Schaafgereedschap
Het wordt sterk aanbevolen om de messen altijd schoon te houden en de katrollen te wassen met een schoonmaakmiddel.
Voer regelmatig een volledige reiniging uit, waarbij tevens een interne smering plaatsvindt
uHydraulische unit
De hydraulische unit heeft geen speciaal onderhoud nodig, maar de volgende instructies moeten worden opgevolgd:
A. Controleer periodiek de olie horizontaal en voeg eventueel olietype toe:
De horizontaal mag niet lager zijn dan 5 cm van de maximale horizontale tank.
Een controle om de 15 werkdagen wordt sterk aanbevolen.
B. Vervang de olie volledig elke 6 maanden of na 630 werkuren.
C. Houd de hydraulische unit schoon en let vooral op de tank en snelkoppelingen.
10.3 Frequente storingsanalyses en oplossing
Tijdens het gebruik kunnen er problemen optreden met de hydraulische unit en de elektrische units. Veel voorkomende storingen worden als volgt weergegeven:
Gebruik bijgevoegd gereedschap, reserveonderdelen of ander gereedschap met een veiligheidscertificaat terwijl u onderdelen onderhoudt of vervangt. Het gebruik van gereedschappen en reserveonderdelen zonder veiligheidscertificaat is verboden.
Storingen in de hydraulische unit | |||||
No | storing | analyseert | oplossingen | ||
1 | De motor werkt niet |
zit los
| |||
2 | De motor draait te langzaam met abnormale geluiden |
| dan 3 MPa
| ||
3 | De cilinder werkt abnormaal |
stevig op slot
| de lucht uit te gaan. | ||
4 | Het slepen van de plaatverplaatsingscilinder werkt niet |
klep is geblokkeerd |
overstroomklep (1,5 MPa is correct).
| ||
5 | Cilinder lek | 1. De oliering is defect2. De cilinder of zuiger is ernstig beschadigd | 1. Vervang de oliering2. Vervang de cilinder | ||
6 | De druk kan niet worden verhoogd of de fluctuatie is te groot | 1. De kern van de overstroomklep is geblokkeerd.2. De pomp is lek.3. De verbindingsspeling van de pomp is los of de sleutelgroef is slip. | 1. Reinig of vervang de kern van het overstroomventiel2. Vervang de oliepomp3. Vervang de verbindingsspeling | ||
7 | De snijdruk kan niet worden aangepast | 1. Het circuit is defect2. De elektromagnetische spoel is defect3. De overstroomklep is geblokkeerd4. De snij-overstroomklep is abnormaal | 1. Controleer het circuit (de rode diode in de elektromagnetische spoel brandt)2. Vervang de elektromagnetische spoel3. Maak de kern van overstroomklep schoon4. Controleer de snij-overstroomklep | ||
Storingen in elektrische eenheden | |||||
8 | De hele machine werkt niet |
| 1. Controleer de voedingskabel2. Controleer de werkkracht3. Open de aardlekschakelaar | ||
9 | Aardfoutschakelaar schakelt uit |
| 1. Controleer de stroomkabels2. Controleer de elektrische elementen.3. Controleer het hogere stroomveiligheidsapparaat | ||
10 | Abnormaal stijgende temperatuur |
4. 4. Mochten de meetwaarden van de temperatuurregelaar hoger zijn dan 300℃, wat erop wijst dat de sensor beschadigd kan zijn of dat de verbinding los zit. Mocht de temperatuurregelaar LL aangeven, wat erop wijst dat de sensor kortsluiting heeft. Mocht de temperatuurregelaar HH aangeven, wat erop wijst dat het circuit van de sensor open is. 5. Corrigeer de temperatuur met de knop op de temperatuurregelaar.
| contactoren
controleur
stel de temperatuur in
contactors indien nodig | ||
11 | Controleverlies bij het verwarmen | Het rode lampje brandt, maar de temperatuur loopt nog steeds op, dat komt doordat de connector defect is of de verbindingen 7 en 8 niet kunnen openen wanneer ze de vereiste temperatuur bereiken. | Vervang de temperatuurregelaar | ||
12 | Schaafgereedschap draait niet | De eindschakelaar werkt niet of de mechanische onderdelen van het schaafgereedschap zijn afgeklemd. | Vervang de planningstoollimiet schakelaar of klein tandwiel |
Diagram van circuit en hydraulische eenheid
11.1 Schakelschema (te zien in bijlage)
11.2 Diagram hydraulische unit (te zien in bijlage)
Ruimtebezettingsgrafiek
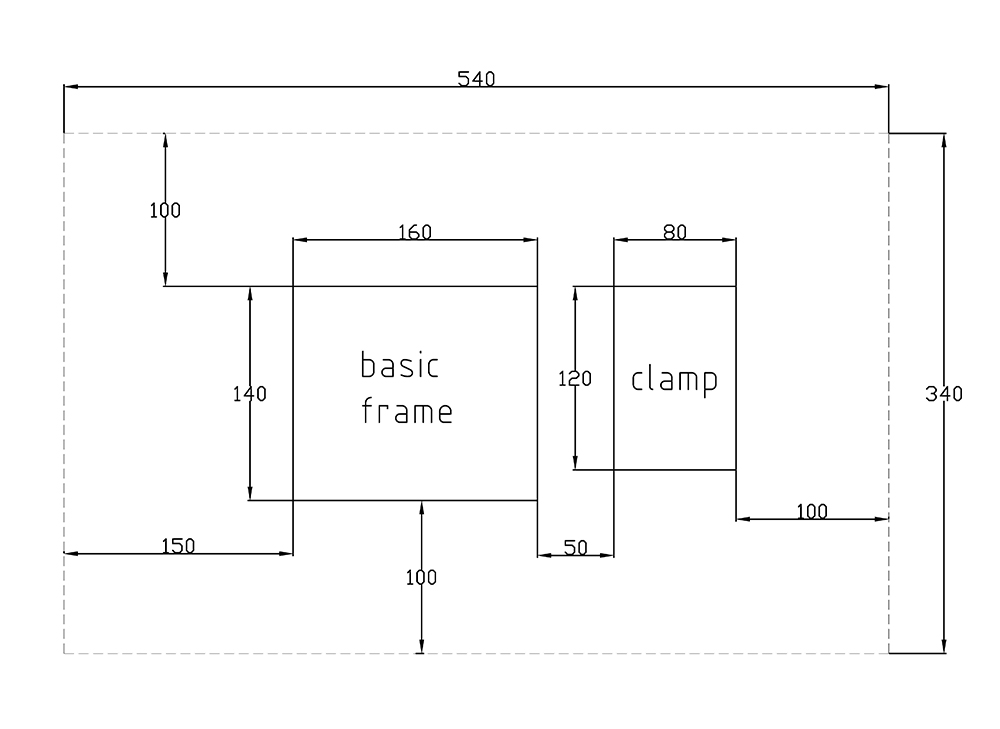