راهنمای عملکرد دستگاه فیوژن TPW200 BUTT
محدوده قابل اجرا و پارامتر فنی
تایپ کنید | TPWS200 |
مواد | PE، PP و PVDF |
محدوده قطر × ضخامت | 200 میلی متر × 11.76 میلی متر |
دمای محیط | -5 تا 45 ℃ |
منبع تغذیه | 220 ولت ± 10 درصد، 60 هرتز |
جریان کل | 12A |
توان کل | 2.0 کیلو وات |
شامل: صفحه گرمایش | 1.2 کیلو وات |
ابزار برنامه ریزی | 0.8 کیلو وات |
حداکثر دما | < 270 ℃ |
تفاوت دمای سطح صفحه گرمایش | ± 5 ℃ |
حداکثر فشار همجوشی | 1040N |
وزن کل (کیلوگرم) | 35 کیلوگرم |
معرفی ماشین
این دستگاه از قاب اصلی، صفحه گرمایش، ابزار برنامه ریزی و پشتیبانی تشکیل شده است.
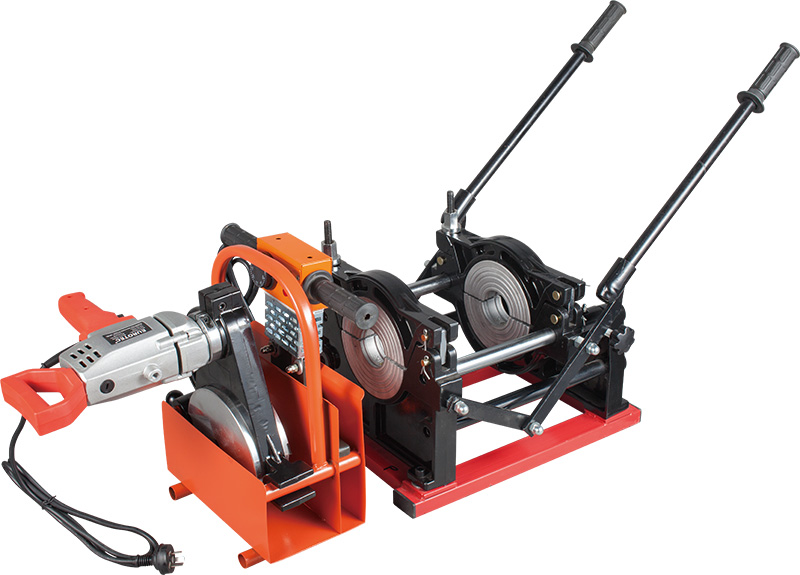
دستورالعمل برای استفاده
5.1 کل تجهیزات باید در یک هواپیمای پایدار و خشک برای کار قرار گیرد.
5.2 قبل از بهره برداری از موارد زیر اطمینان حاصل کنید:
منبع تغذیه مطابق با دستگاه فیوژن لب به لب مشخص شده است
خط برق خراب یا فرسوده نیست
تیغه های ابزار برنامه ریزی تیز هستند
همه سازها عادی هستند
تمامی قطعات و ابزار لازم موجود است
دستگاه در شرایط خوبی است
5.3 درج های مناسب را با توجه به قطر خارجی لوله / اتصالات قرار دهید
5.4 روش جوشکاری
5.4.1. قبل از جوشکاری، ابتدا بررسی کنید که آیا خراش یا شکافی روی سطح لوله ها / اتصالات وجود دارد یا خیر. اگر عمق خراش ها یا شکاف ها از 10 درصد ضخامت دیوار بیشتر شد، خراش ها یا شکاف ها را بردارید.
5.4.2 سطح داخلی و خارجی انتهای لوله جوش داده شده را تمیز کنید.
5.4.3 لوله ها / اتصالات را قرار دهید و طول کشیده لوله ها / انتهای اتصالات را که باید جوش داده شوند برابر (تا حد امکان کوتاه) نگه دارید. برای کاهش اصطکاک، انتهای دیگر لوله باید توسط غلتک ها پشتیبانی شود. پیچ های گیره را ببندید تا لوله ها / اتصالات را ثابت کنید.
5.4.4 ابزار برنامه ریزی را قرار دهید، آن را روشن کنید و انتهای لوله ها/اتصالات را با قرار دادن دو میله درایور روی ابزار برنامه ریزی ببندید تا زمانی که براده های پیوسته و همگن از هر دو طرف ظاهر شود. قاب را جدا کنید، ابزار برنامه ریزی را خاموش کنید و آن را بردارید. ضخامت براده باید بین 0.2 تا 0.5 میلی متر باشد و می توان آن را با تنظیم ارتفاع تیغه های ابزار برنامه ریزی تنظیم کرد.
6.4.5 لوله ها / انتهای اتصالات را ببندید و تراز را بررسی کنید. ناهماهنگی نباید از 10% ضخامت دیوار تجاوز کند و با شل کردن یا سفت کردن پیچ های گیره می توان آن را بهبود بخشید. شکاف بین دو انتهای لوله نباید از 10% ضخامت دیوار تجاوز کند. در غیر این صورت لوله ها / اتصالات باید دوباره برنامه ریزی شوند.
5.4.6 گرد و غبار و شکاف روی صفحه گرمایش را پاک کنید (لایه PTFE را روی سطح صفحه گرمایش خراش ندهید).
5.4.7 صفحه گرمایش را پس از بدست آوردن دمای مورد نیاز در قاب قرار دهید. فشار را تا زمانی که مهره به ارتفاع مورد نیاز برسد، با عمل بر روی دسته بالا ببرید.
5.4.8 فشار را به مقداری کاهش دهید که به اندازه ای باشد که هر دو طرف با صفحه گرمایش برای مدت زمان مشخص تماس داشته باشند.
5.4.9 وقتی زمان تمام شد، قاب را جدا کنید و صفحه گرمایش را بردارید، دو طرف را در اسرع وقت به هم وصل کنید.
5.4.10 فشار را افزایش دهید تا مهره مورد نیاز ظاهر شود. دستگاه قفل را ببندید تا مفصل به خودی خود خنک شود. در نهایت گیره ها را باز کنید و لوله اتصال را خارج کنید.
5.4.11 اتصال را به صورت بصری بررسی کنید. محل اتصال باید تقارن صاف باشد و پایین شیار بین مهره ها نباید از سطح لوله پایین تر باشد. ناهماهنگی دو مهره نباید از 10 درصد ضخامت دیوار تجاوز کند، در غیر این صورت جوشکاری بد است.
استاندارد جوشکاری مرجع (DVS2207-1-1995)
6.1 به دلیل تفاوت در استاندارد جوشکاری و مواد پلی اتیلن، زمان و فشار در مراحل مختلف جوشکاری متفاوت است. این پیشنهاد می کند که پارامترهای جوش واقعی باید توسط سازنده لوله ها و اتصالات ارائه شود.
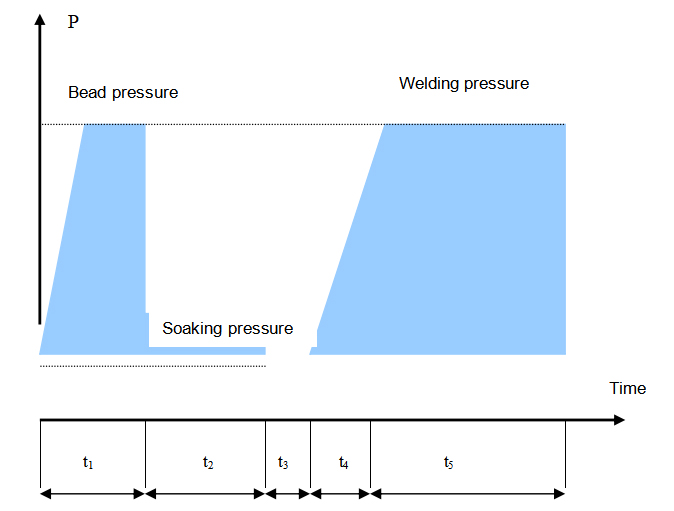
ضخامت دیوار (میلی متر) | ارتفاع مهره (mm) | فشار ایجاد مهره (MPa) | زمان خیساندن t2(ثانیه) | فشار خیساندن (MPa) | تغییر در طول زمان t3(ثانیه) | زمان افزایش فشار t4(ثانیه) | فشار جوش (MPa) | زمان خنک شدن t5(دقیقه) |
0 تا 4.5 | 0.5 | 0.15 | 45 | ≤0.02 | 5 | 5 | 0.15±0.01 | 6 |
4.5 تا 7 | 1.0 | 0.15 | 45 تا 70 | ≤0.02 | 5 تا 6 | 5 تا 6 | 0.15±0.01 | 6 تا 10 |
7 تا 12 | 1.5 | 0.15 | 70 تا 120 | ≤0.02 | 6 تا 8 | 6 تا 8 | 0.15±0.01 | 10 تا 16 |
12 تا 19 | 2.0 | 0.15 | 120 تا 190 | ≤0.02 | 8 تا 10 | 8 تا 11 | 0.15±0.01 | 16 تا 24 |
19 تا 26 | 2.5 | 0.15 | 190 تا 260 | ≤0.02 | 10 تا 12 | 11 تا 14 | 0.15±0.01 | 24 تا 32 |
26 تا 37 | 3.0 | 0.15 | 260 تا 370 | ≤0.02 | 12 تا 16 | 14 تا 19 | 0.15±0.01 | 32 تا 45 |
37 تا 50 | 3.5 | 0.15 | 370 تا 500 | ≤0.02 | 16 تا 20 | 19 تا 25 | 0.15±0.01 | 45 تا 60 |
50 تا 70 | 4.0 | 0.15 | 500 تا 700 | ≤0.02 | 20 تا 25 | 25 تا 35 | 0.15±0.01 | 60 تا 80 |
نکته: فشار ایجاد مهره و فشار جوش به شکل فشار رابط توصیه شده است، فشار گیج باید با فرمول زیر محاسبه شود.
عبارات:
فشار جوش(Mpa)=(مقطع لوله جوش ×0.15 N/mm2)/(2 ×8×8×3.14) + فشار را بکشید
اینجا1 مگاپاسکال= 1 N/mm2